Effects of CO2 gas in Mig/mag welding
Currently, CO2 gas is being commonly used in the MIG - MAG welding process, especially when welding medium carbon steel. The reason CO2 is popular is because of its reasonable price and ability to create stable welds, meeting mechanical standards even when welding at high speeds and with deep weld seams. However, do you really understand the role and properties of CO2 in MIG - MAG welding technology?
Contents
Overview of MIG/MAG welding method
MIG/MAG welding method belongs to the GMAW welding group, using heat from a metal arc in a protective gas environment, also known as wire welding or CO2 welding. This heat source is continuously supplied through the wire feeder at a stable speed, helping to maintain the welding process effectively.
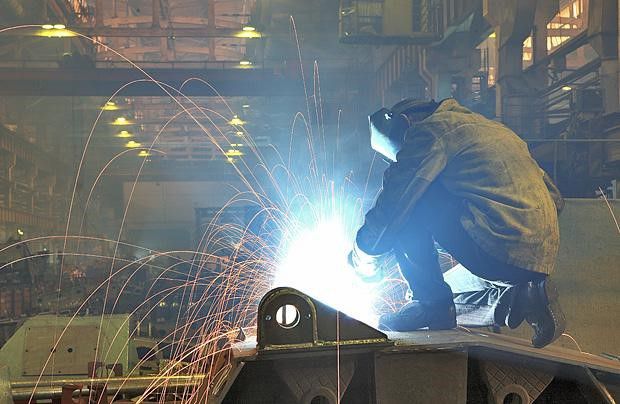
MAG welding is commonly applied to common structural steels, stainless steels, heat-resistant steels, hot-strength steels, as well as special alloys such as aluminum, magnesium, nickel, copper, and reactive alloys. Strong with oxygen. This is a popular technology in both automatic and semi-automatic welding, providing high flexibility in many applications.
The special thing about MIG/MAG welding is that it can be performed in any spatial position and is compatible with many types of welding machines in Vietnam, from arc welding machines to mini stainless steel welding machines. However, in the construction industry, this method is rarely used outdoors because air flow can affect the shielding gas and weld quality.
How does CO2 gas affect MIG/MAG welding?
CO2 gas is a compound consisting of one Carbon atom and two Oxygen atoms, usually existing as a gas in the atmosphere. Carbon dioxide can exist in three states: gas, liquid, and solid. This is a common gas in nature, produced from processes such as fire or respiration.
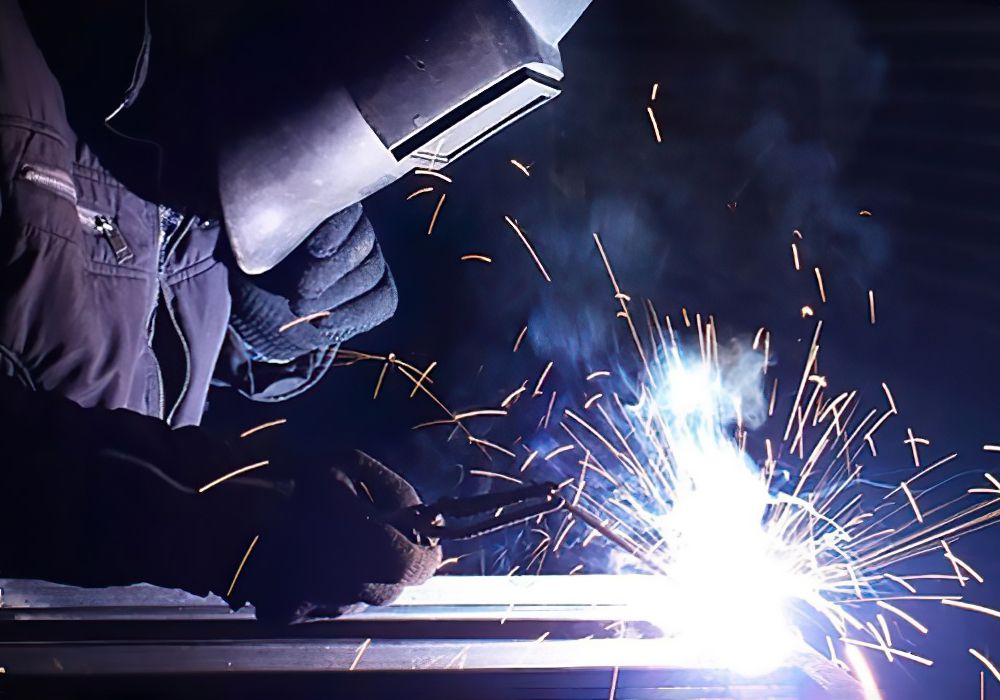
CO2 gas has many applications in life, from beverage production, beer and wine production, food preservation, to medical fields such as surgery and endoscopy. In industry, it is widely used, especially in MIG/MAG welding.
In MAG welding, CO2 is often used to weld medium carbon steel. However, the disadvantage of CO2 is that the spray metal transfer is not coaxial and the arc bridge transfer process can be unstable, easily causing metal splashing. Because CO2 is oxidizing in the arc, it decomposes into CO and O2, which requires the electrode to contain suitable deoxidizers to ensure a porosity-free weld.
Refer to MIG/MAG welding machines here
The reason why CO2 gas is often used in MIG/MAG welding
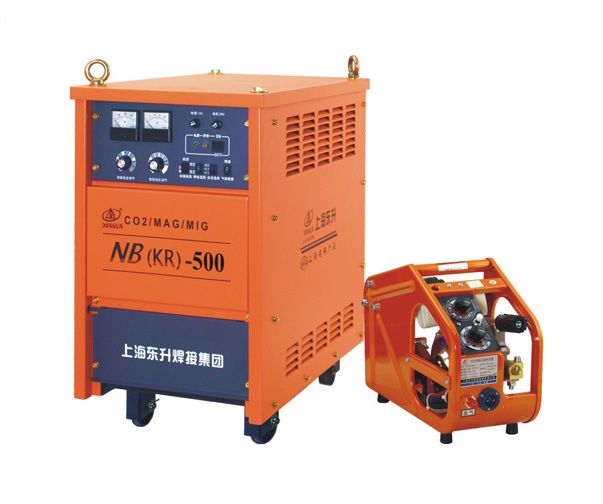
CO2 gas is very popular, easy to find and has low production costs. Thanks to this property, CO2 is widely used in many fields, including industrial welding.
CO2 gas welding brings high productivity, about 2.5 times superior to the manual arc welding method. This helps increase work efficiency, especially in projects that require high speed.
Compared to arc welding under the flux layer, welding in CO2 gas is more technologically advanced because it can be performed in many different spatial locations, bringing flexibility during the construction process. Besides, thanks to the fast welding speed and concentrated heat source, the weld quality is high, with less warping and the heat-affected zone is also narrower, helping the product achieve high precision.
In addition, working conditions when using CO2 welding method are also improved. The welding process does not generate toxic gases, ensuring worker safety, making this method more user-friendly than manual arc welding.
Address to buy genuine Mig welding machines
EMIN is a unit specializing in providing industrial gases for metal cutting and welding processes. With stable supply and guaranteed quality, we are committed to always fully meeting customer needs, bringing peace of mind about product source and quality.
Reference: JASIC alternating MIG welding machine