Electronic engineering for beginners
When starting to learn electric welding techniques, there are many questions that are asked and a common one among them is "Why does the rod always stick and can't come out when welding?" Even if you try to continue working, the welding machine is at risk of overheating due to overload. The article below will help you answer this question.
Contents
Causes of solder stick sticking
Why do welding rods often stick when welding? This is a problem that many people who are new to welding often encounter. To solve it, we need to find out the main causes and how to fix them.
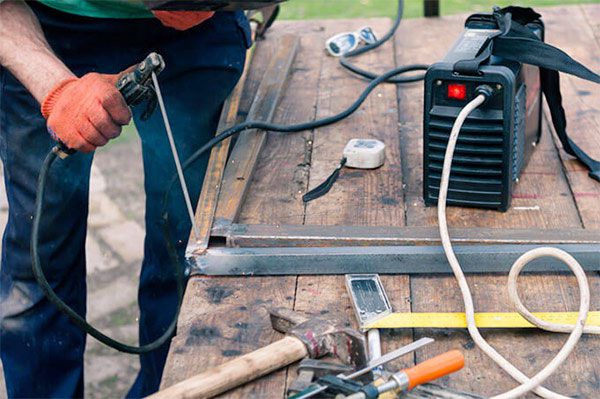
-The current is not at the correct level
Adjusting the current is very important when welding. If the current is too weak, the welding rod will easily stick, the weld will not be tight and there will be slag. On the contrary, too strong a current can splash material or even puncture the weld, especially with thin plates. Therefore, you need to check and adjust the current to suit the thickness of the welding object and the type of welding rod being used.
- Inappropriate selection of welding rods
Each type of solder requires a different type of welding rod. For thick materials, you should use welding rods with larger diameters. If chosen incorrectly, the welding rod will not only damage the material but also directly affect the quality of the weld. Always refer to technical information to choose the right type of rod.
- Poor quality welding rods
Welding rods that do not meet standards or are damp or broken in the coating are also reasons that make the weld unsightly and prone to errors. To avoid this, you need to store the welding rod in a dry place, away from high humidity. If the welding rod is damp, dry it before use to ensure the best quality weld.
- The distance between the welding rod and the solder object is not correct
When welding, keeping a suitable distance between the welding rod and the welding object is a necessary technique. If the distance is too close, the rod will stick to the solder. On the contrary, if it is too far, the arc cannot be stable. So, practice keeping the distance even and correct throughout the welding process.
Electric welding technique
Learning electric welding techniques requires time and steady hands. While instructional materials may provide a theoretical foundation, true mastery comes from hands-on experience. Here are some basic tips to make soldering easier:
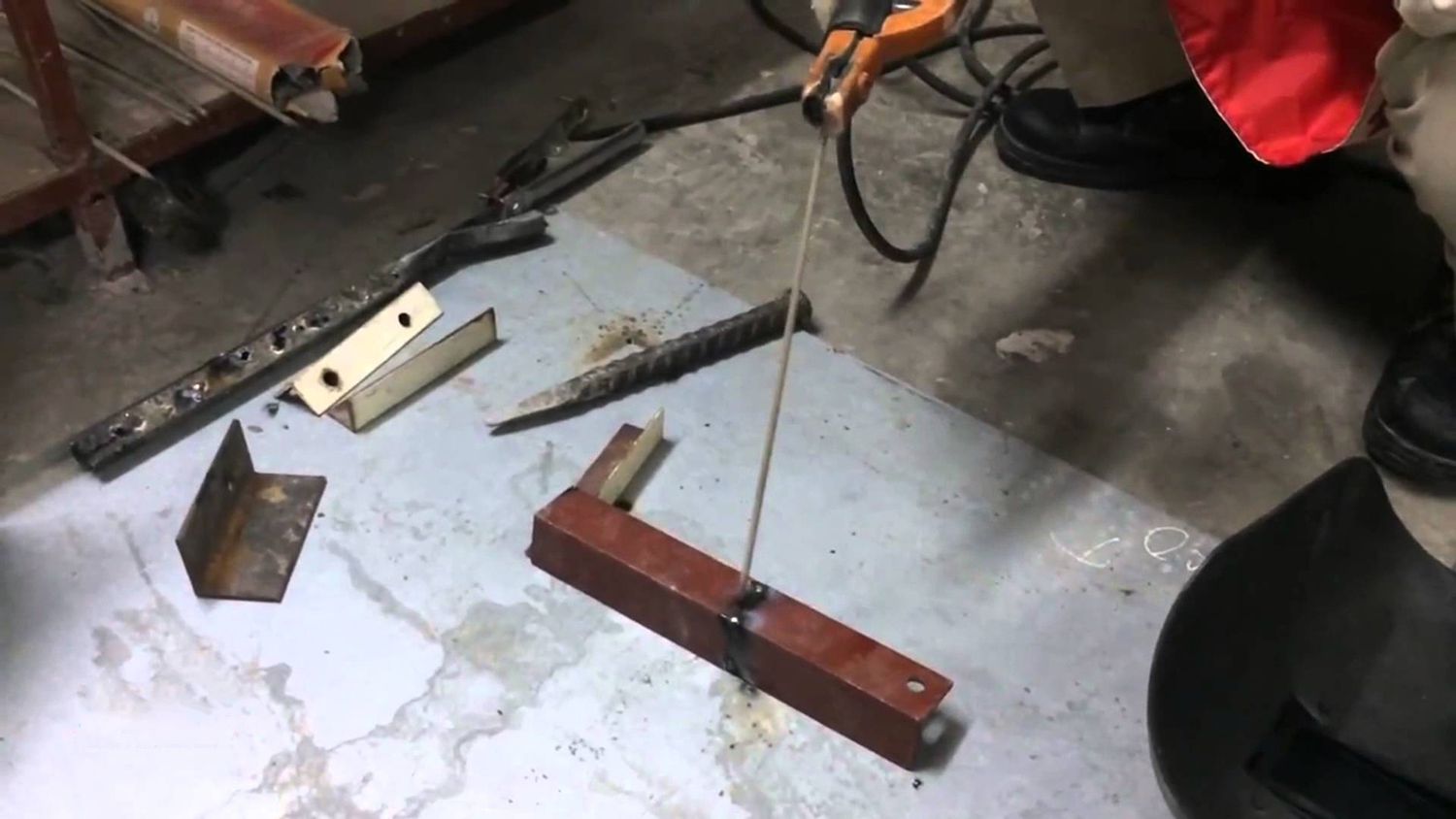
- Adjust the welding position for more convenience
When welding in an L-shaped corner, try to place the welded object so that it forms a V-shaped corner (if conditions allow). This method helps keep the weld in a horizontal position, reducing difficulty in manipulation and ensuring a more even and beautiful weld.
- Clean the weld before starting
To ensure good contact, the weld needs to be cleaned before performing. Remove paint, dirt or rust from the surface of the material. If working with zinc-coated iron, you should grind off the zinc layer in the area to be welded. In particular, when welding multiple passes, tap and brush off the slag layer on each weld pass before proceeding to the next to avoid affecting quality.
- Choose the appropriate welding rod
The type of welding rod used will largely determine the quality of the weld. Choose a welding rod that matches the thickness of the material and the specific technical requirements of the job. Choosing the right one will help the welding process go smoothly and the weld will meet better standards.
Instructions for choosing the right welding rod for the welding machine
Choosing a welding rod depends on the thickness of the material and should be suitable for the type of welding machine you are using. A correct choice will help the welding process be more efficient and the weld will achieve the best quality. Below are suggestions for combining welding rod diameter and suitable welding machine:
- Welding rod diameter 1.6mm - 3.2mm:
These welding rods are suitable for welding machines such as HK 200A, HK 200E, and HK 200Z. In particular, these machines can still pull welding rods with a diameter of 4.0mm if needed.
- Welding rod diameter 3.2mm - 4.0mm:
For larger welding rods, use the HK 250T or HK 250TP welding machine. These are machines that can handle well at this diameter range.
- Welding rod diameter 4.0mm - 5.0mm:
Larger welding rods require a more powerful machine, like the HK 315, HK 315i or HK 400i. If needed, these machines can even pull welding rods up to 6mm in diameter.
Basic steps to learn electric welding
If you are new to electric welding techniques, start by preparing the following basic steps to easily grasp and practice effectively.
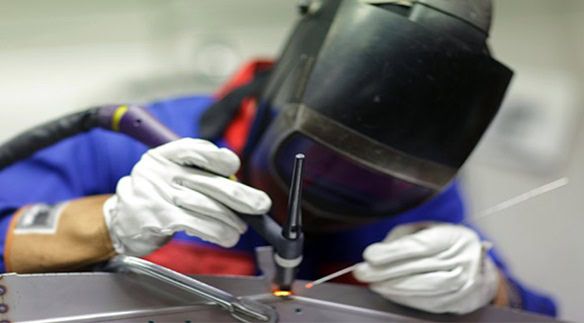
First of all, you need to prepare all the necessary equipment. A suitable electric welding machine, welding rods, welding mask, protective gloves and protective clothing are indispensable items. In addition, make sure you have carefully read and understood the welding machine instructions before starting, to ensure safety during the process.
Once you have all the equipment, you can start choosing the right welding materials to practice with. Materials such as steel, aluminum or copper are good choices, and you should prioritize material sheets with a thickness of about 3-6mm for easy control when first learning to weld.
Next, setting up the welding equipment is an important step that cannot be overlooked. Adjust parameters such as current intensity, welding speed, material thickness and welding rod type to suit the material and technical requirements. This helps ensure the welding machine operates stably and the weld is of the best quality.
When everything is ready, you can start welding. Work slowly and steadily, focusing on creating the weld point by point. This not only gives you better control but also ensures a beautiful and durable weld.
Welding technique is the key factor that determines weld quality. When first learning, you need to pay attention to factors such as material thickness, welding rod type, and operating speed. Focusing on performing the correct technique will help you quickly get used to it and progress.
To become a good welder, regular practice is essential. Spending time every day practicing not only helps you improve your skills but also builds confidence when working.
Finally, take the time to learn more about the basic principles and techniques of welding. This knowledge will help you better understand the work you are doing and apply it more effectively in practice.